Oracle's Construction Tech Lab Eases Path to Innovation
In the 21st century, we are exposed to many things in our lives that are the result of innovation: smartphones, electric or driverless cars, renewable energy, smart homes, Internet streaming services and gaming, mobile apps and digital ordering, medical testing and treatments, resilient agriculture, online banking and fundraising through crowdsourcing.
And while many people use their smartphones to order almost anything they want or stream a movie, that may not transfer into a desire to transform their residence into a smart home or resort to online banking. We all have a certain level of comfort with new technology and ideas, and sometimes it’s hard to get over the trepidation to start something different.
The construction industry also has seen its share of innovation with the use of connected devices, virtual reality/augmented reality, drones and robotics, building information modeling and 3D scanning, to name a few. But facility managers and contractors have the same dilemma: How do they evaluate what is not only practical for their companies but getting employees out of their comfort zones to properly use new technologies?
This is where the new Oracle Construction and Engineering Innovation Lab comes in. Located outside Chicago in Deerfield IL, it is a 15,000-sq-ft simulated worksite that demonstrates to contractors, facility managers and other construction industry professionals how these technologies work — and work together — to make jobsites safer and workers more productive. As a result, construction professionals can determine what techniques will work the best within their companies.
They also can discover how to communicate with their partners more effectively. A smooth project results when owners, engineers, contractors and subcontractors truly work together as partners.
The idea for the facility came about a year and a half ago, says Burcin Kaplanoglu, the Innovation Lab’s executive director. The explosion of digital products for use in building construction over the last year or so threatens to overwhelm already-busy construction professionals.
“We needed space to try [out technologies] in the physical environment,” he notes. “Not in the conference room, but actually out [in a simulated construction environment] and try it. If you want to solve problems on a worksite, you actually have to do it yourself. Until you physically do it, you’re not going to see what comes out of it.”
Oracle surveyed its industry customers, who were enthusiastic about the idea of hands-on experience with up-and-coming tech products. So, the outdoor lab — ready to be outfitted with sensor and automation technologies — was assembled in Deerfield, not far from O’Hare Airport. It resembles a typical construction jobsite where people can experiment with different products and see how those products fit in with their company goals. Kaplanoglu says that, as far he knows, Oracle is the only tech company in the construction engineering space with a lab like this.
“It’s hard to innovate when you’re running projects,” he explains. “Because you’re doing day-to-day operations, you’re busy. A lot is going on and trying new things is challenging. So having a simulated worksite allows you to try products before you put them on an actual worksite. That’s one angle.”
Solving Real Problems
The other part of the Innovation Lab equation focuses on construction professionals themselves. How can new tech help elevate contractors and facility management personnel?
“We’re a technology company; we’re here to provide the tech,” Kaplanoglu notes. “And tech is moving really fast. We all know that. The real improvement has to be in the process and the skills of the people to achieve the results we want. The lines between the digital and the physical world are blurring.
Having a physical worksite, working with our customers and partners, allows us to improve the processes and also improve the skills of the people.”
As the idea of the lab progressed, Oracle took an approach to it that you might not expect. “We didn’t start with the tech; we started with the problems,” Kaplanoglu explains. “We went to customers and asked, ‘What do you want us to solve?’”
Out of those customer conversations came five common areas providing challenges to construction professionals:
- Worker safety. Keeping workers safe on the jobsite is a top priority in the industry;
- Material tracking. One pain point is knowing whether material has been delivered on-site and where it is located, Kaplanoglu says;
- Progress reporting. How can we do it right to ensure the right people get the correct data?;
- Remote operations or assistance. Kaplanoglu notes that to help counter the skilled labor shortage in the industry, we need to centralize operations;
- Visualization. This is where virtual reality and augmented reality come into the picture, Kaplanoglu says.
“It goes back to the process and the people,” he explains. “Do you really need to do this in 10 steps? Can you do it five? Then if it’s five, what technology can help you? How do we need to modify it to make five? Next month, can you do it in four steps? And how do we train people to do it in four? It all ties together.”
Kaplanoglu believes the Innovation Lab cannot only upskill the current construction workforce, it also can help bring new blood into the industry. “Spaces like this can enable us to recruit new talent to industry — showing that it can be high tech and productive, and you can still go home in a reasonable time and feel less stressed,” he explains.
High stress is another problem for the industry, he says — many people leave the construction industry because of high-pressure levels and stress-related medical issues and don’t return. “Using technology to reduce the number of steps in a certain process — and do it accurately and reliably — can reduce stress levels and provide a good work-life balance.”
Efficiency for Today
The lab officially opened in August 2018 and has since seen “hundreds of hundreds” of visitors, Kaplanoglu says. “It has been a fascinating journey. We didn’t have to do much; the industry recognized there is a niche for it. We just came up with an idea, executed it and it took on a life of its own as it evolved.”
He adds that while the Innovation Lab can illustrate future technologies, the drive behind it is to show engineers and contractors tech that is available today to make their projects more reliable and efficient.
“We can share with you what the future work site is going to look like,” he says. “But 80 percent of the technologies we have here on the site are commercially available. It’s what one of our customers calls ‘reality-driven innovation.’ We want people to come here and see things, like them and say, ‘I want to try this because this is going to help my work next week.’ Not five years from now.
“Yes, we do have information on 5G data and AI. And people want to hear the thought leadership, to understand where the industry is and what those things will do. That’s great. But it’s not something you can do tomorrow. It’s not something that will help your business today.”
Whether a customer is going to purchase a specific technology comes down to two words, Kaplanoglu says: cool and like.
“When people look at something and say, ‘That’s cool,’ what I’ve learned is they’re not going to do it,” he notes. “When people look at something and say, ‘I like it,’ I know they’re going to try it. So we’re going for a little bit of cool, but mostly likes.”
He says more than half of the people who go through the lab end up buying something they’ve tried and implemented it into their business. Of course, it depends on resources, type of projects, timing, etc. And Kaplanoglu acknowledges that people coming through the lab are already predisposed to using technology to make changes.
But sometimes those progressive professionals bring “naysayers” with them. “They realize they can use this space as a vehicle to show those naysayers how the tech works,” he adds. “In some cases, the naysayers will actually [use the tech] themselves. And they may be more open to it because they physically tried it.”
One area Kaplanoglu would like the lab to look into is prefabrication, or what he calls industrialized construction, which is about streamlining processes. “Why are we going to keep doing this process over and over again on the jobsite?” he asks. “You can do it in a controlled factory environment instead.
We are looking into that space, how it ties to the worksite itself.”
In a controlled environment, workers can assemble panels or equipment parcels at the same time every time, resulting in predictable, reliable results.
“For us, we see a tremendous value on the mechanical and plumbing systems,” Kaplanoglu notes. “Industrialized construction can have a tremendous impact on the productivity, safety and the lives of the people who are doing the work. And technology is here to help.”
Sidebar: Lab Partners
Below, a sample of the vendors who have so far supported the facility:
• Assemble
• Bosch
• Here
• ITI
• Jovix
• nPlan
• Realwear
• Reconstruct
• SmartVid.io
• Triax
About the Author
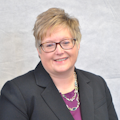
Kelly L. Faloon
Contributing Writer/Editor
Faloon spent 3 1/2 years at Supply House Times before joining the Plumbing & Mechanical staff in 2001. Previously, she spent nearly 10 years at CCH/Wolters Kluwer, a publishing firm specializing in business and tax law, where she wore many hats — proofreader, writer/editor for a daily tax publication, and Internal Revenue Code editor.
A native of Michigan’s northern Lower Peninsula, Faloon is a journalism graduate of Michigan State University. You can reach her at [email protected].